How to build a digital twin?
What is a digital twin?
The idea of digital twin technology was first expressed in 1991 with the publication of Mirror Worlds by David Gelernter. However, it was Michael Grieves who first applied the concept of digital twins to manufacturing in 2002 and officially announced the concept of digital twin software. Since then, digital twins have become more widely used and are now an important component of corporate design in many fields: construction, energy, industry, healthcare and many others.
A digital twin can be described as a virtual replica of a process, product or service. This virtual replica “feeds” on the data of the asset it represents thanks to its sensors but also sends back other data to optimise it. Digital twins are particularly associated with the term “industry 4.0”, which corresponds to a new way of organising production resources by merging the virtual world, digital design and management with real-world products and objects. A new era of “smart production” where machines could handle production in an intelligent way to maintain profits while reducing production (e.g. robots could be connected directly to the order book to manufacture products only in the configurations ordered, reducing stock and unsold products but improving the potential for customisation).
In this article, we will look in detail at how to build a digital twin from scratch (or from 01000001 to 01011010 if you are a machine).
Step 1: Create a blueprint
Before even starting to create the digital twin, you need to define its purpose. A digital twin must be able to be integrated into the decision-making process as well as into the production optimisation process. The digital twin must therefore be reusable (multiple uses), scalable (easy to improve over time) and provide value through its use.
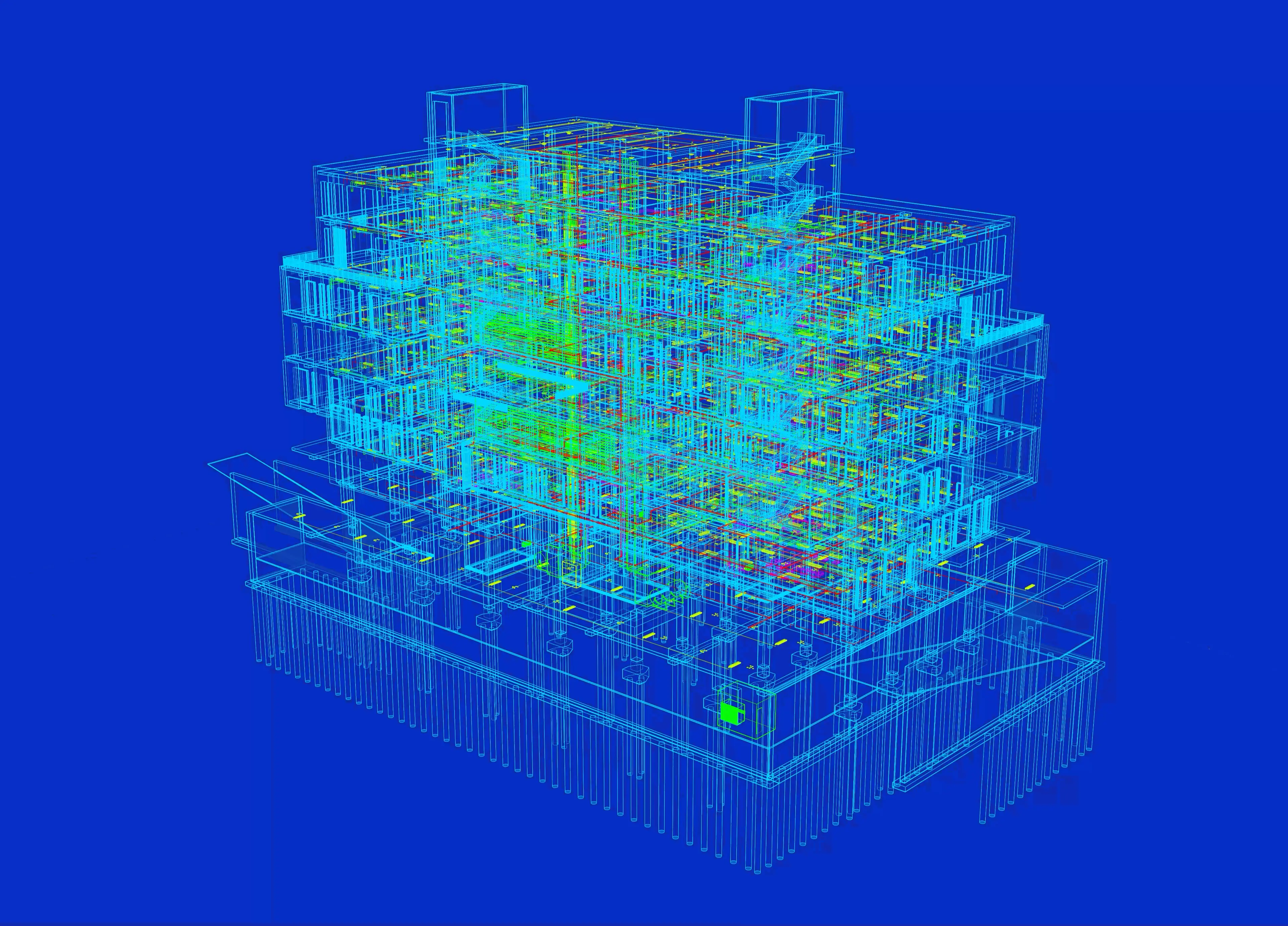
Step 2: Structure the data
As explained at the beginning of this article, the digital twin is built from real world data to work with real world data. Thus, it is necessary to sort and structure the data that will be used to create the digital twin. This step is very time consuming as the data is often different and independent and therefore not ready to be used to create the digital twin. This is a task that can take several months and is carried out by data scientists and data engineers, but it has a crucial role to play in ensuring the quality and usability of the data. The better the data used, the closer the digital twin will be to the asset it represents.
Step 3: Create the digital twin
To proceed with the creation of the digital twin, we need to link real-time data provided by sensors via the Internet of Things to feed our virtual replica. At this point, the digital twin is “alive” and communicating in real time with its real counterpart, but this communication is only one-sided for the moment, since the digital twin only receives data in real time without sending back other data to optimise processes. Thus, the goal will be to simulate scenarios to find possible points of improvement so that the digital twin helps its counterpart in its operation.
The most visually impressive part is the creation of a three-dimensional physical environment in which the digital twin will be placed. This requires a scanning process to generate a 1:1 model. There are two ways of doing this, the first is to have a person with specialised equipment move around the environment of the digital twin, taking photographs of the area from several angles. The second option is to use specialised 3D software for creating virtual spaces such as Nvidia Omniverse where there is no need to move someone around as the virtual environment can be created directly via real-world measurements and via the library of resources included in the software.
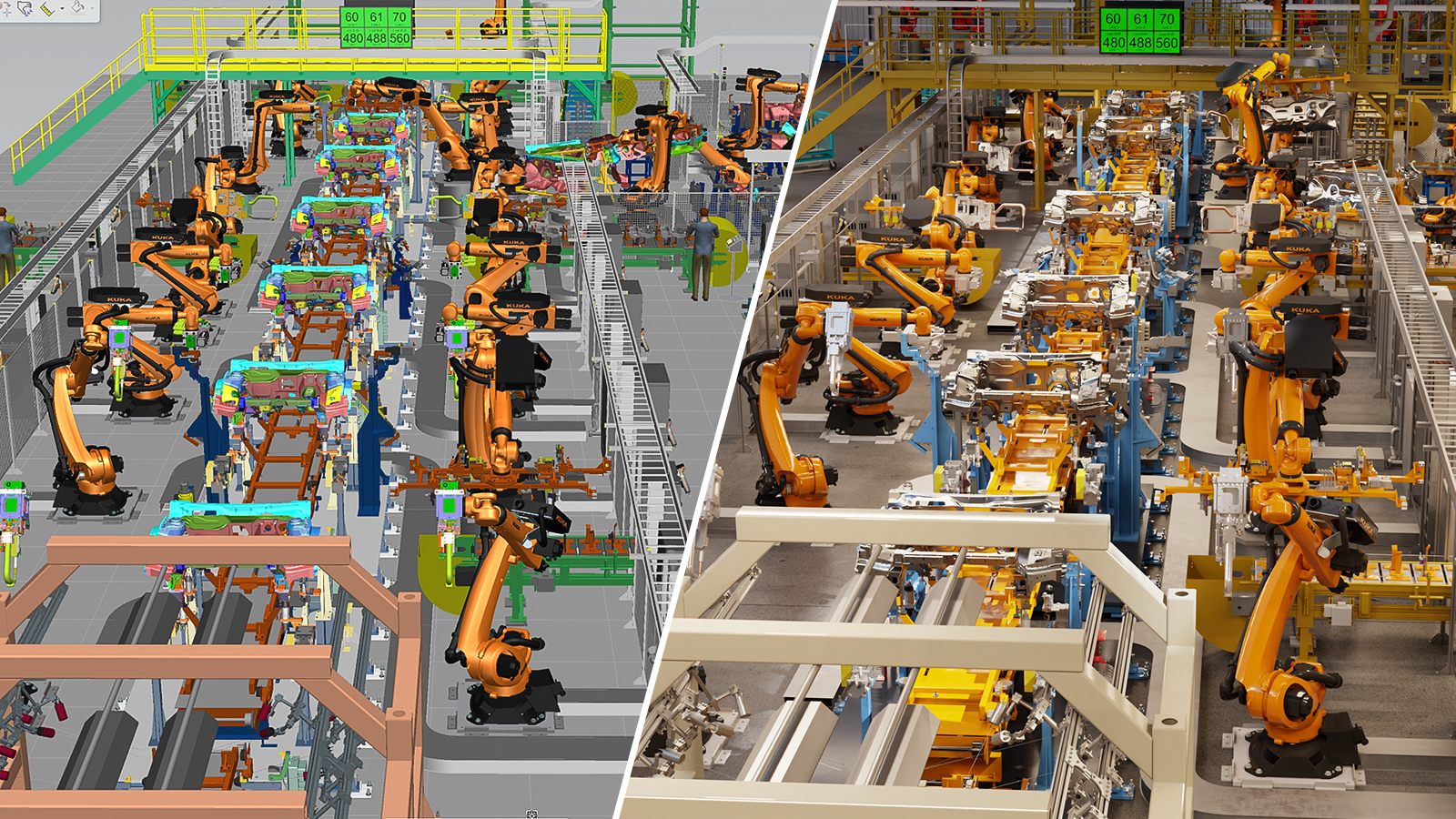
Step 4: Enhance the capabilities of the digital twin
A digital twin in its environment is good, but the next step in this development is to be able to integrate real-time data that does not come from the real world asset but from other sources. This can be data from sensors through the Internet of Things such as small connected weather stations, data from other assets that are themselves connected whether or not they are in the same business as your asset (e.g. the location of ships carrying your goods to predict their arrival date). This data enhances the capabilities of the digital twin by integrating it fully into the value chain to which it contributes (e.g. a bicycle factory is at the centre of the value chain as it receives raw materials such as aluminium and ships bicycles). The ability to connect the different stages of the value chain within the same digital twin allows the performance of the real asset to be optimised according to the events that occur upstream or downstream of it.
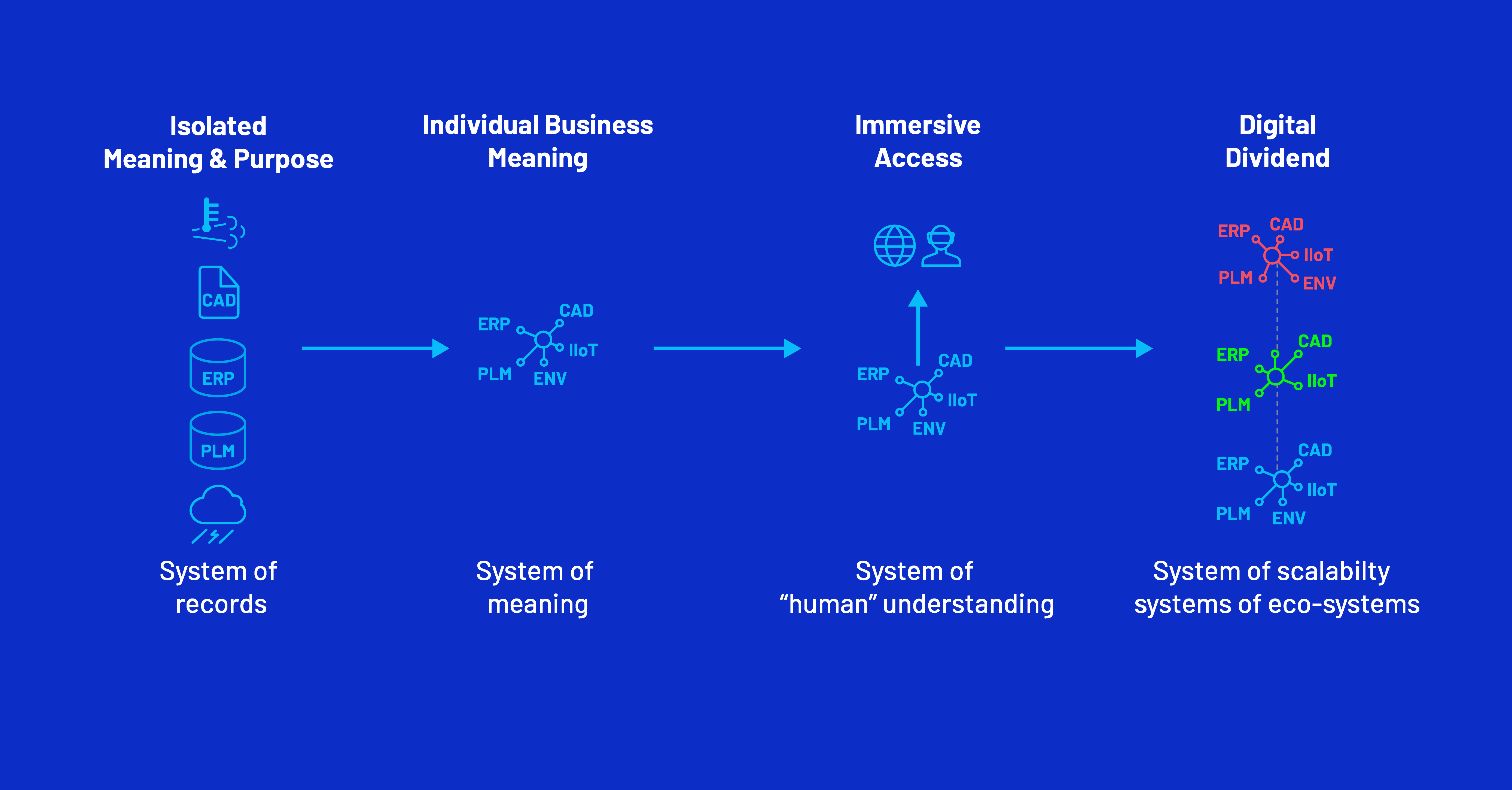